On time, on budget: Extractly delivers dust extraction system for new factory
- PWT
- 5 hours ago
- 4 min read
Extractly Limited recently completed the installation of a 20,000m³/hr dust waste extraction system – with a super-quick turnaround – for a leading furniture manufacturer
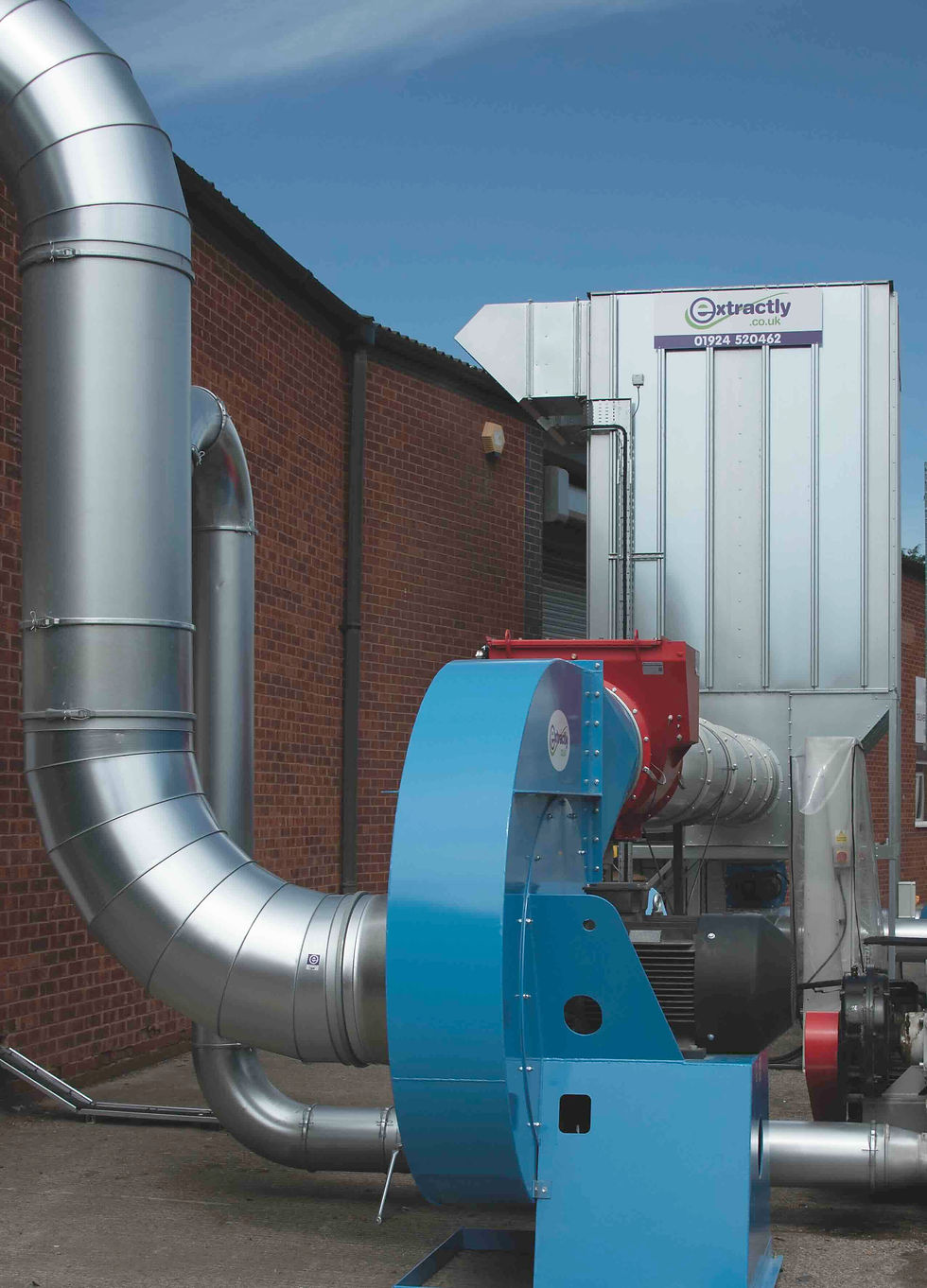
Established in 2015 by Managing Director Martin Clarke, Cotswold Panel Products Ltd manufactures bespoke panel components and produces panel-based built furniture for the hospitality, events and exhibition markets; corporate office spaces; educational establishments; as well as POS items for retail businesses and other specialised commercial sectors.
With Martin at the helm, the company remains very much a family-run business, renowned for quality, attention to detail and delivering a high level of customer service with a personal touch.

Company relocation
Over the past decade, Martin’s dedicated team has continually driven the company forward, achieving consistently solid sales growth. This growth has demanded a continuous programme of investment in cutting-edge machinery to deliver ever-greater capacity, which, in turn, has necessitated bigger and better premises to house it all. The company’s latest plans involved moving production just over the border – around seven miles as the
crow flies – from a semi-rural site in Gloucestershire to a new 20,000sq.ft facility on the north-west outskirts of Evesham in Worcestershire.
“Our relocation has actually been on the cards for around two years,” Martin explained. “Unfortunately, plans to move to another property we’d earmarked fell through at a late stage; we’d even got as far as going out to tender for the installation of a new dust extraction system.” Extractly Ltd had previously carried out a relatively minor addition to the extraction system at the company’s former location. Impressed with the service provided and the engineers’ work on site, Martin had included Extractly Limited on the shortlist for the new system.
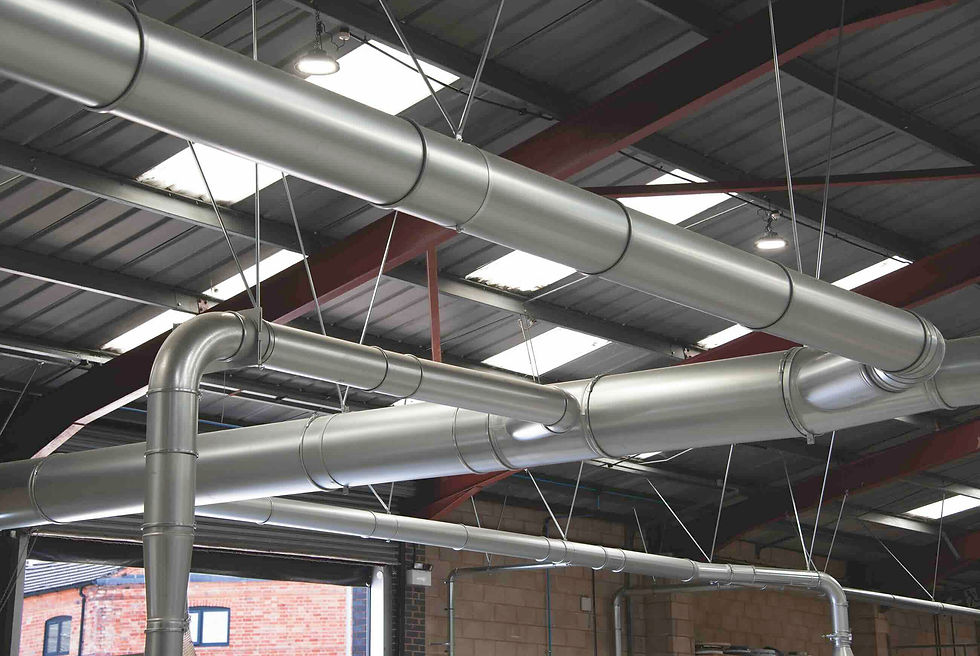
New proposal from Extractly
Although that move was ultimately scuppered, the decision had already been made to award the contract to Extractly, based on their industry knowledge, understanding of the requirements, proposed budget and commitment to meeting a tight deadline. “So, when the Evesham property came across our radar at the beginning of the year,” Martin continued, “I was more than happy to invite Extractly to put together a new proposal, based on our updated requirements.”
“We were delighted to have another opportunity to work with Cotswold Panel Products,” says Graham Seymour, Extractly’s sales engineer on the project. “And this installation was straight out of the textbook.” The new location allowed production flow to be organised much more effectively and provides plenty of capacity to increase output and accommodate future machinery acquisitions.
“The factory was being completely refurbished ahead of the move,” says Graham. “So, with no production schedules to work around, we had virtually free rein to install the most efficient extraction system to meet the demands of the company’s current range of high-speed machinery, with a margin of spare capacity for future expansion.”

A neat & efficient installation
The system currently extracts from an externally sited chipper, along with 10 other production machines of varying capacity – from edge sander to edgebander, drilling machines to CNC machining centres. The main 45kW fan delivers dust- and chip-laden air to the Aagaard ASF 2 DAK XL ATEX filter unit, which houses over 160m³ of filter material to capture extracted wood waste from the airflow.
Heavier waste material drops into the hopper section at the unit’s base, where it’s continually gathered by scrapers on a chain conveyor. Above the filtration section, three 1.5kW regeneration fans operate intermittently to remove finer dust from the filter material. All collected waste is discharged pressure-free via a rotary valve, from where a 15kW waste transport fan delivers it to a sealed waste container ready for its final journey to a biomass energy plant.
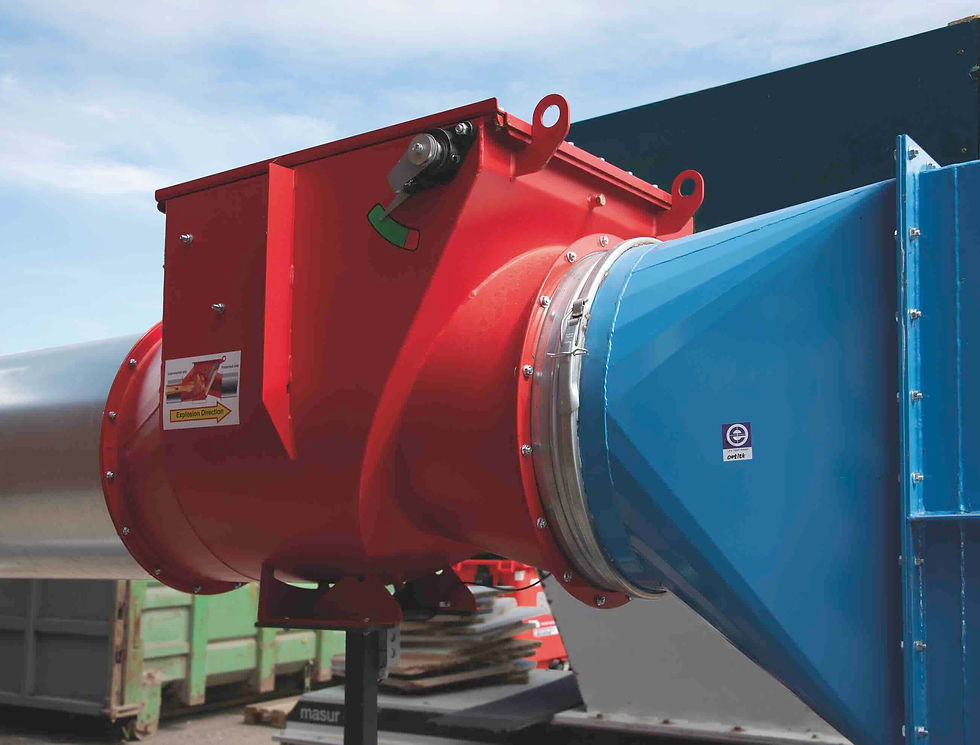
Nordfab’s QF galvanised steel ductwork connects all machines to the extraction system. In the unlikely event of an explosion in the filter unit, an ATEX-certified non-return valve ensures that pressure and flames are prevented from travelling back down the ductwork and into the factory.
“Extractly executed a really neat and efficient installation for us,” Martin concludes. “I couldn’t fault the professional manner in which the project was delivered. The entire installation was completed in under a week, allowing us to move straight in with machinery and get back to full production in under 10 days.”
For further information on Extractly Limited, call 01924 520 462, email info@extractly.co.uk or visit the website: www.extractly.co.uk.